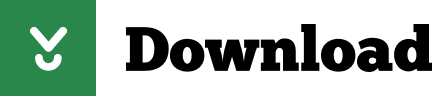
With Fluid Dynamics Engineer, simulation technologies are connected with SOLIDWORKS® and PLM, thanks to the 3DEXPERIENCE Works connection, leveraging a single collaborative environment for end-to-end product development. This allows designers and engineers-even simulation novices-to innovate simulation-driven designs. It enables users to quickly explore hundreds of designs while concurrently improving product performance. The solution leverages industry-standard, RANS-based finite volume CFD technology with a fully guided user experience. Fluid Dynamics Engineer is tailored for engineers who perform routine fluid flow and conjugate heat transfer calculations to guide design improvements while exploring innovative design concepts. This typically takes several months, followed by physical testing. In a typical design process for flow and thermal systems, designers or engineers create 3D models, which are then sent to a specialist for computational fluid dynamics (CFD) analysis and simulation. Possessing this information early in the design cycle can reduce costs while improving performance and quality. Fluid Dynamics Engineer enables design engineers to carry out high-fidelity internal and external fluid flow and thermal simulations, delivering actionable information to improve products while they are designing them.Īccess to fast, accurate fluid flow solutions allows you to evaluate multiple designs. It allows for evaluating optimal flow distribution, efficient thermal management, minimal pressure losses, and other performance criteria early in the design cycle. The Fluid Dynamics Engineer Role, part of the 3DEXPERIENCE® Works portfolio, provides fluid flow and thermal analysis simulations to help guide the design process for SOLIDWORKS® designers and engineers.
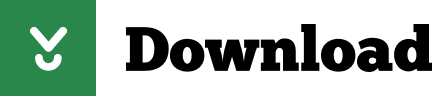